There's something magical about watching a surfboard take shape from raw foam. In our Austin workshop, master shaper Carlos Rivera approaches each blank with the reverence of a sculptor approaching marble. This isn't just manufacturing – it's an art form that bridges ancient tradition with cutting-edge design.
The Foundation: Understanding the Foam
Every great surfboard begins with quality foam. We source our blanks from trusted suppliers who understand that the core of a board determines its soul. The density, the grain, the way the foam responds to the planer – these details matter more than most riders realize.
"I can tell within the first few passes of the planer whether a blank has the right character," Carlos explains, running his hands along the rough-cut foam. "Some blanks want to be performance shortboards, others are calling out to be classic logs. My job is to listen."
The Dance of Design and Function
Modern surfboard design is a delicate balance between tradition and innovation. We study classic shapers like Skip Frye and Maurice Cole, but we're not afraid to push boundaries. Our design process involves extensive computer modeling, but the final shaping is always done by hand.
The rocker – the curve from nose to tail – determines how the board will feel in the water. Too much, and you'll lose speed. Too little, and you'll struggle in steep waves. It's a dance between physics and intuition that takes years to master.
Tools of the Trade
Our workshop is filled with both traditional hand tools and modern machinery. The electric planer removes the bulk of the foam, but the final shaping is done with hand tools that haven't changed much in 60 years. There's a reason for this – the human touch can feel inconsistencies that machines miss.
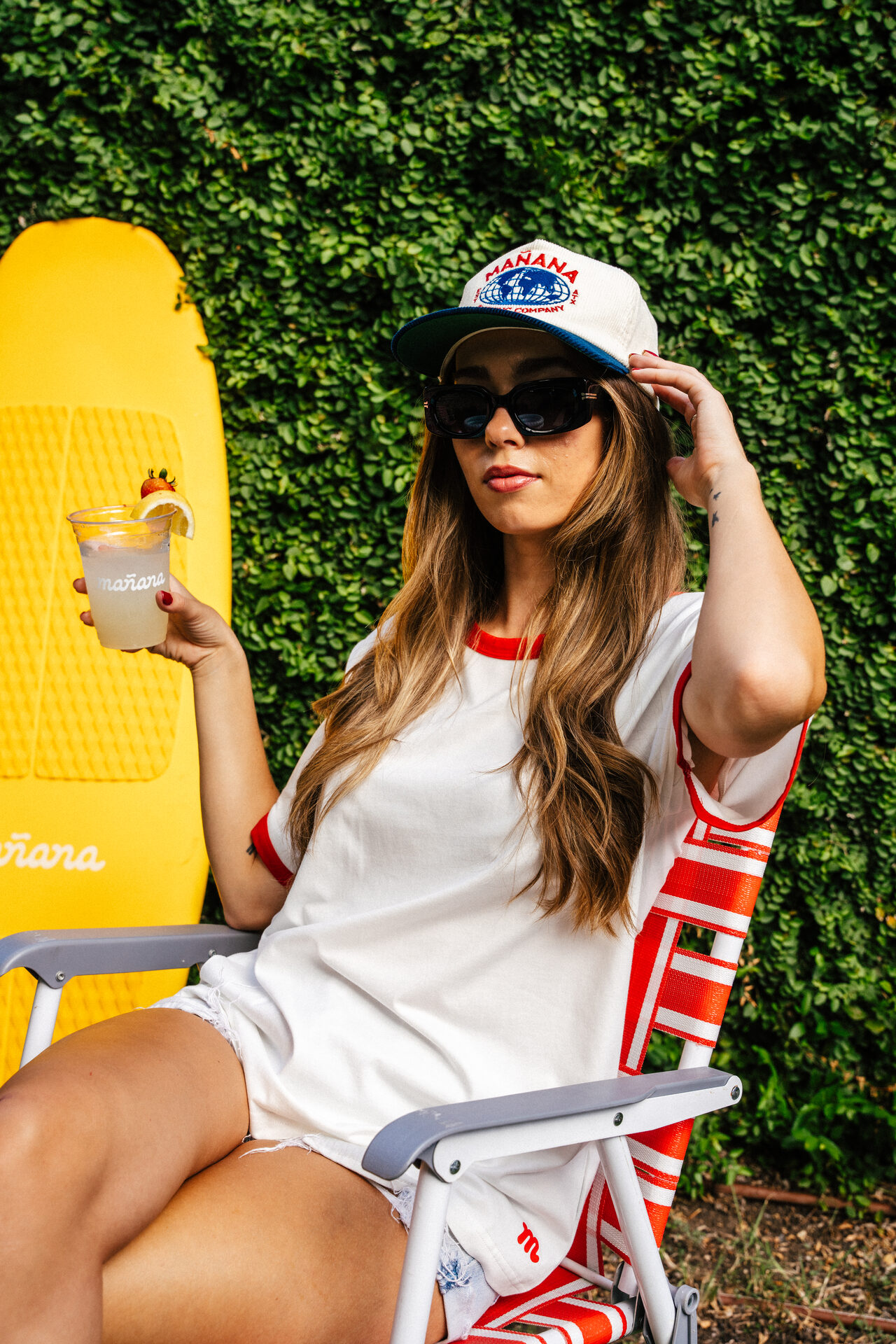
The sanding process is where the magic really happens. Starting with 60-grit and working up to 220-grit, we slowly reveal the true shape of the board. Each pass of the sandpaper is deliberate, purposeful. This is where patience becomes a virtue.
The Glassing Process
Once the foam is shaped to perfection, it's time for glassing. This is where the board gets its strength and its shine. We use premium resin and carefully selected fiberglass cloth, applied in multiple layers for maximum durability.
The lamination process requires perfect timing and temperature control. Too hot, and the resin will cure too quickly. Too cold, and it won't cure properly. It's a process that demands both technical skill and artistic vision.
The Final Touch
The final sanding and polishing is where the board truly comes alive. This is where we add the gloss that makes the colors pop and the grain of the wood stringers shine through. It's labor-intensive work, but the results speak for themselves.
When we hand a finished board to a customer, we're not just selling a piece of equipment – we're passing on a piece of functional art that will carry them across countless waves. That's the true soul of surfboard shaping.